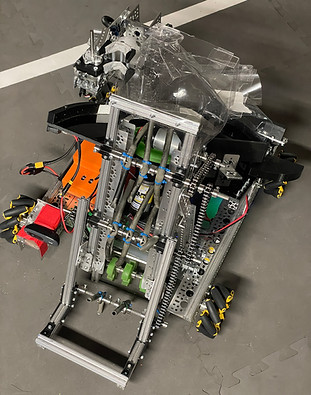
Pond
FTC ā2020 - 2021
ā
2021's first robot, Pond, was built to compete in the Ultimate Goal challenge presented by Qualcomm. In autonomous, our robot is able to drop the wobble goal in the specified box and park. In the driver-controlled period, our robot has the capabilities to collect four rings.
Design Process
Throughout the season, our team faced many challenges mechanically for the robot. Each mechanism on the robot presented its own unique requirements that the team had to think critically about. To progress development of the robot, the team used many engineering principles from experts and established companies.
ā
The V shape of the Systems Engineering Principles represents the ideals that our team bases development off of. It is necessary to dig downward and lay a large foundation in order to build upward and make the tallest structure in the world. This was used in the robot design as the team was able to plan out items with CAD software before assembling them.

KISS (Keep it Simple Silly) was one of the many design process principles our team members learned in FLL from the NASA Jet Propulsion Lab (JPL). This idea is essential to our team's design process as it pushes us to focus on efficient, achievable designs. The simpler the mechanism, the easier to maintain. With simple mechanisms there are also less points of failure.
ā
Parallel Prototyping is the concept of making additional prototypes while keeping the original intact. This allowed our team to divide up work among all members so everyone can actively work on the robot. This also allows the team security because if one item doesn't work, we can fall back on the last working design.
ā
Our mentors' experience in working on space programs and national systems has shown us that failure is not an options. It is extremely important to maintain Fail Safes/Recovery Functions in all aspects of our robot. We learned how to program autonomous functions with contingency options in place. There are timers placed in each part of the program to ensure that, if the robot gets stuck in the program, the robot would be forced to stop and continue to the next part of the program. This guarantees that the robot will attempt all autonomous tasks.
ā
Being well-versed in the mission and priority is critical in planning tasks during the season. Mission Strategy Development also helps us to focus on certain tasks and guide trade studies forward.
In order to align the team, it was necessary to have individual team members identify their goals for the robot at the beginning of the season. Over a few weeks and with multiple iterations, team members presented Preliminary Design Reviews to show a combination of the best designs that would achieve the game tasks. Design reviews provide end-goal of design reviews is to recognize ideal mechanisms, robot requirements. design reviews to present a combination of the best designs the team had come up with for the previous weeks and to identify a path for the team to take to construct a competitive robot.
ā
Mechanical Overview and Evolution
For the drivetrain this year, our team decided to use a stock GoBuilda drive base for simplicity and maneuverability. With this, we could focus on other components and easily mount them on the pre designed drivetrain.
The collector design was built so that a ring could quickly move up a track and be deposited into a magazine for the shooter. This was accomplished through a two C-channel design that pushed the rings upwards and then down a chute into the magazine.
ā
The shooter was built around a 6000 rpm GoBuilda motor. The design is built so that the motor can drive the flywheel directly, and the rings can have as much contact with the wheel as possible. With this design, we realized that the vibrating motor caused a lot of inconsistency, so we needed to externally mount the motor next time.
ā
In the first version of our robot, the design for the wobble goal collector was primarily a basic claw mechanism. The wobble goal could be grabbed tightly and efficiently with this simple design. Though, there were some major problems with the design: there was not enough tolerance in the claw, so major precision necessary. We planned to fix this as we designed the next iteration of this collector. For the second version, we took an inspiration from our Relic Recovery block collector. Utilizing compliant wheels and the friction they provide, we built a mechanism with two servos, custom 3D printed parts, and 4 compliant wheels, designed to suck in a sandwich the pole of the wobble goal.



Software Overview
The software system is divided into three broad parts: the position tracking system, the computer vision system, and the path implementations. In addition to this, the auxiliary system responsible for controlling the shooter to make it shoot more smoothly.
The position tracking system does what its name implies; that is, it uses input from multiple sensors to maintain a record of the robot’s coordinates and heading across the field at the present moment.
ā
The computer vision system is a collection of computer vision detectors that can be switched on and off, depending on whether they are needed at a certain point during program execution.
ā
The path implementations are the highest level “main” OpMode files. They are referred to as path implementations because it is here that the lower level components (to command the robot where to go and what to detect) are put together and commanded to embark upon a certain path.
ā
As of now, the shooter currently uses a simple PID controller to keep the speed constant as it shoots rings.